
INDUSTRIES
INDUSTRIES

We would love to discuss your next project WITH YOU
252.975.3101
SERVICES
Carver Machine Works is an engineering centered, disciplined metal fabricator.
Providing customers with:
-
Outstanding service
-
Seamless integration of various projects:
-
Design-to-build prototypes
-
Large weldments that require post-weld precision machining
-
Component refurbishment
-
Pump rebuild and assembly
-
Design validation services for our customers to finalize their engineering needs, utilizing both SolidWorks & AutoCAD
-
Project Management | Precision Machining Waterjet Capabilities
Mechanical Assembly, Dynamic Balancing, Field Installation
Fabrication | Quality | Welding Processes & Certifications
Equipment Refurbishment
Project Management
Project Engineers and Project Managers offer design validation services, reverse engineering experience and design improvement recommendations for easier manufacturability, reducing costs increasing the quality of the final product.
​
Our customers turn to CMW when they:
-
Need industry expertise to determine a rebuild/refurbish scope of work
-
Require reverse engineering know-how to reduce budget costs and lead time
-
Must have design validation services for a design conception to a plan to manufacturability
-
Need qualified industry experts to determine cost saving recommendations without compromising quality
​
Precision Machining
Waterjet Capabilities
We have the master craftsmen and machining equipment to handle the most stringent tolerances and machining challenges.
Our equipment includes:
-
3 Horizontal Boring Milles (HBMs) with 4″ to 6″ spindles
-
7 Engine Lathes ranging up to a max swing of 63″ x 312″ overall length
-
3 Vertical Turrent Lathes (VTLs) with up to a 79″ swing
-
HAAS CNC 3-axis Milling Center
-
2 Manual Milling Center
-
OMAX 55100 Waterjet Machine with a 50″ x 100″ x 6-1/2″ thickness cut capacity
-
Faro Arm CMM with 6′ swing
Our craftsmen are cross-trained to run many of our machines.
​
See our HAAS CNC Lathe in Action!
​
​
​
​
Mechanical Assembly
Dynamic Balancing
Field Installation
MECHANICAL ASSEMBLY
CMW mechanical assembly services have been one of our biggest value creators for our customer’s needs to lower their budget and decrease lead time. As an extension of our equipment refurbishment, including our dynamic balancing capability, we are able to bring pumps, blowers and other rotating equipment back to life and last as long as a new, far more expensive component.
How our mechanical assembly process works:
-
Perform the disassembly
-
Clean the components in preparation of a condition inspection
-
Quality Inspectors will perform a condition inspection and create a condition report
-
Our experienced Project Management team will evaluate the condition report and create an estimate to rebuild
-
CMW will submit a quoted scope of work
-
Once the purchase order is received from our customer we begin our overhaul
-
Our typical lead time to rebuild a pump or blower is 8-12 weeks
DYNAMIC BALANCING
Offering static and dual plane dynamic balancing. Balancing reduces vibration improves bearing life and reduces structural stress on your equipment. Our machines are soft bearing systems and can balance up to six feet in diameter and weight up to 5,000 pounds.
Balancing is essential to most all rotating equipment including:
-
Process Roll and Shafts
-
Impellers
-
Rotors
-
Fans and Blowers
-
Centrifuges and Mixers
-
Gears and Drive Shafts
Benefits Include:
-
Less wear to bearings, shafts and rotors
-
Reduced energy costs
-
Few machinery breakdowns and loss of production
-
Efficient operation of machinery
-
Extended overall life of equipment
Certified balance reports are available upon request on all fabricated and refurbished equipment.
​
FIELD INSTALLATION
CMW offers field services that include removal of your current pump, installing a rebuild, alignment, and routine maintenance.
​
Welding Processes
& Certifications
With a full arrangement of standard welding processes and an extensive list of qualified welding procedures, CMW is capable of complying with almost any requirement in a variety of industry standards. Our welding processes include:* Gas Tungsten Arc Welding (GTAW) also known as Tungsten Inert Gas (TIG)* Gas Metal Arc Welding (GMAW) often referred to as Metal Inert Gas (MIG)* Flux Core Arc Welding (FCAW)* Shield Metal Arc Welding (SMAW) or Stick Welding* Submerged Arc Welding (SAW)We have also incorporated semi-automated weld processes to reduce cost and improve quality into our welding processes.We concentrate on a full arrangement of processes and standards to best meet the need and functionality of customer’s needs for their projects.
Fabrication
Utilizing SolidWorks, AutoCAD and our dedicated team of engineers and draftsmen, we work to our customer’s as early as the conceptional phase of the project. We partner with our customers to transform these initial designs into final designs that incorporate our extensive fabrication experience to improve the form, fit and function of the component.
​
Quality
-
CWI (Certified Weld Inspector)
-
Our NDT capabilities include:
-
In house Level 1 & Level 2 – VT and PT
-
Level 3 – VT, PT, UT, RT and MT
-
AS9100 total quality system & continuous improvement program developed proven fabrication processes
-
Ensure proper training
-
Supervision
-
Material tracking
-
Segregation of operations
-
Accountability to effectively produce repeatable quality
-
-
We have extensive experience and are actively involved throughout:
-
Contract review
-
Specification evaluation
-
Procurement flow down requirements
-
Design and design change control
-
Planning
-
Manufacturing
-
Gas Tungsten Arc Welding (GTAW) also known as Tungsten Inert Gas (TIG)x*
-
Gas Metal Arc Welding (GMAW) often referred to as Metal Inert Gas (MIG)*
-
Flux Core Arc Welding (FCAW)
-
Shield Metal Arc Welding (SMAW) or Stick Welding
-
Submerged Arc Welding (SAW)
Equipment Refurbishment
Whether your capital equipment has long lead times, expensive replacement costs or individual parts are obsolete, CMW possesses the ability to refurbish your existing equipment. We offer our services to be a cost effective alternative to an OEM while providing improvements that will extend the life of your equipment and reduce or eliminate operational down time.
We restore your equipment by incorporating our expertise in:
-
REVERSE ENGINEERING
We restore your components to save you you money and time compared to OEM prices and lead-time. -
WELD REPAIR
Effective weld processes that restore worn areas from fluid cavitation, excessive vibration, abrasion and general wear through our proven weld build up practices. -
MACHINING
Once the worn areas have been restored through our weld repair processes, we utilize our precision machining capabilities to restore your equipment to their original dimensions. -
DYNAMIC BALANCING
-
Static and dual plane dynamic balancing to reduce vibration and therefore:
-
Extend bearing life
-
Reduce structural stress on your equipment
-
Our machines are soft bearing systems and can balance up to six feet in diameter and weight up to 5,000 pounds
-
CMW also offers certified balance reports upon request on all fabricated and refurbished equipment
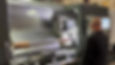